Diatomite production at Toomebridge
The extract below has been sourced from the 'family.kiwicelts.com' website and they acknowledge their source as below in bold text
Quiet Places of the Lower Bann Valley was published by the authors John Hughes and Donal Barton of 36 Mosside Road, Dunmurry, Copyright Reserved. 2004
Diatomite was first discovered in lands adjoining the River Bann in the townland of Ballynease near Portglenone in or about the year 1855. Locally it was referred to as Bann Clay and used in the manufacture of bricks for the building trade, known as Culbann Brick.
In 1898, the Grant Brothers of Toomebridge on finding deposits on their lands, took its uses further, in that they developed its insulating properties. The machinery used to reduce the Diatomite to powdered form was housed in a factory erected by them on a site situated to the rear of where the present RUC Station now stands. They operated a successful business here until 1914 when they sold out to the United Kingdom Peat, Moss, and Litter Co. Ltd., which was owned by a Mr. James Stott, an Englishman who settled in Toome and on his death was laid to rest in Duneane Parish Graveyard.
At this juncture "The United Kingdom Peat Moss and Litter Co. Ltd" was sold to a company named Kenyon who were involved in insulation. This change took place during 1947.
In 1968 Jack McBride, a 'Glens Man ',who was attached to the Ballymena Observer and who finished his days in the newspaper profession with the Irish News, describes in an article his introduction to Diatomite. It was while out walking near Toomebridge, he noticed several men engaged in what seemed to be turf cutting and as he approached the bank he was surprised to see the 'turf' were a whitewash colour and stacks nearby were even whiter.
On enquiring, "What sort of peat is that?" He was informed rather sharply by one of the cutters, "That's not peat, that's Diatomite!" or what is pronounced "Kieselguhr" in German. Kiesel means gravel and Guhr is earthy sediment fermentation. Going on, he begs to be excused for becoming a bit technical as he explains that Diatomite is an unusual kind of stuff. In the first place, Diatoms are microscopic unicellular plants belonging to algae, a class of flowerless plants living mostly in water, seaweed and the green scum found on ponds being the best known.
Diatoms are also distinguished by the complex structure of their cell walls, which are usually strongly impregnated with silica, a flinty mineral that, next to oxygen, constitutes about 27% of the earth's crust. The individual cells of Diatoms are called frustules and, in fossil form are generally white or grey in colour, and resemble clay.
They are used as polishing powders, absorbents for nitro-glycerine in the manufacture of dynamite and are used in the preparation of some of the best dentifrices. Their principal use is now in the making of non-conducting and soundproofing materials.
Jack McBride, who went for a walk along the banks of the River Bann, thinking Diatomite was turf, ended up with a great deal of knowledge on the subject.
The Quinn Family have been for many years involved in mining, milling and marketing of Diatomite and the business of producing and marketing sphagnum peat. Prior to the arrival of the United Kingdom Peat Moss and Litter Co. Ltd., from England in 1913 this family had been involved in the manufacture and marketing of' Culbann Brick '. The Quinns joined the recently arrived company and over the years, three brothers namely Patrick, Frank and Dan and later Dan's son Frank Junior gave excellent service in promoting its interests. Dan was responsible for the production of sphagnum moss, while Frank had charge of the Diatomite business, he was also a Director and General Manager of the United Kingdom Peat Moss and Litter Co. Ltd. Frank retired in 1968 and was succeeded by his nephew Frank Junior who had joined the company in 1958 and who managed the business until his retirement in 1995.
The United Kingdom Peat Moss and Litter Co. Ltd. began business in the area in 1913 and as we already know, they opened up several bogs for the manufacture of sphagnum peat moss. They also began digging, harvesting and milling Diatomite, but within a short space of time, their deposits of this mineral had been used up. To remain in business they purchased deposits and a factory belonging to the Erin Diatomite Co. Ltd., of Glasgow, which was then based in the townland of Glenone close to Portglenone. Such was the demand for this product, that within a short time these deposits ran out.
Frank Quinn the Company's General Manager then began a search for larger and better quality seams of Diatomite. In this he had much success, as he found a large areas of the mineral in the townland of Creagh, together with deposits on land belonging to Mr. Hunter of Brecart, also on lands the property of Frank, Neill and John Grant all of Toomebridge. In addition to obtaining a lease on all these deposits, he purchased the Grant Brothers factory and as a result, the company moved headquarters from Glenone to outside Toome. In addition to the discoveries already mentioned, valuable areas of Diatomite were located in the townlands of Kermegran, Aughnahoy, Tyanee, Lislea, Portglenone, Gortgole and Tamlaght, all of which border on the River Bann.
The clay when properly dried was transported from these outlying fields by boat along the River Bann to the sand quay at Toomebridge. The vessel, named The Slaney, had a carrying capacity of 100 tons and was crewed by John Francis Doherty and Harry Downey. The cargo was unloaded by crane onto horse and carts and in later years tractor trailers and taken to the factory for grinding. The transport to the docks in Belfast was initially by rail and later by lorries belonging to the Ulster Transport Authority, from there the Diatomite was shipped to England.
Production peaked during the years of the Second World War at 6,000 tons per annum, this was made up by 4,000 tons milled and 2,000 tons dug, bagged and exported direct from the clay fields and known as wet clay. Due no doubt to competition from new products arriving on the market, demand for Diatomite by 1968 had fallen to 2,000 tons, by 1994 it was down to 600 tons. In the later years in an effort to sustain production, insulation products were manufactured at the factory. With the company's remaining deposits in the area beginning to diminish, it was decided to cease operations. So after a period of almost 80 years, production of Diatomite came to an end. During those years a workforce of approximately 20 people were employed on a full time basis, rising to over 100 during the spring and summer months. This helped to boost the local economy especially in the lean years between the two world wars when employment in the area was almost non-existent.
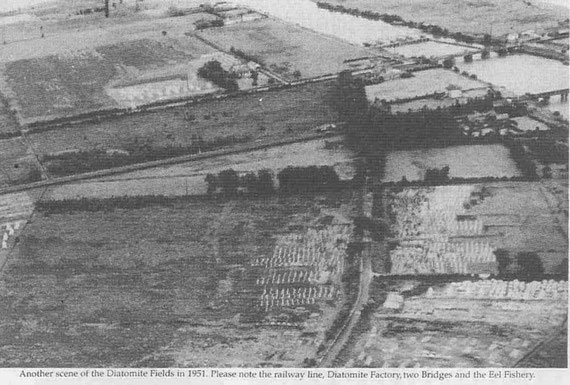
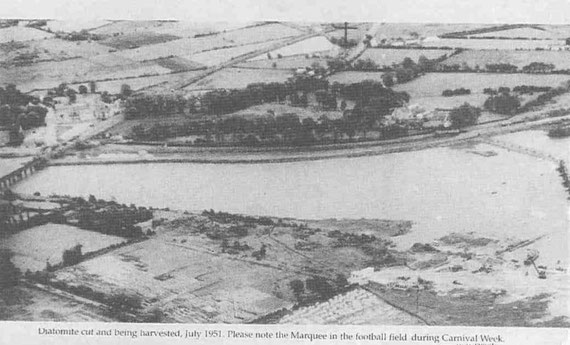